30 January 2022
4min read time
Brooke Payne
i-spraywash Active Foam Vs Regular Foaming Guns
Share:

The i-spraywash produces a unique foaming system called Active Foam.
There are many industrial foam cleaning systems on the market; however, most miss the mark when it comes to optimal results. Wastage of chemicals – and time – are two key drawbacks, both of which are due to less-than-desirable problems with foaming.
The i-spraywash, hailed as being faster, cleaner, greener, safer and more ergonomically friendly than most conventional foam cleaners, also boasts one fundamental difference – it produces a unique foaming system called Active Foam.
Introducing Active Foam
i-spraywash is specifically designed to create a very fine foam bubble. This bubble is barely visible, so compared to conventional foaming equipment, the i-spraywash may be deemed to ‘not foam as well’. However, there is a specific reason why the i-spraywash ‘Active Foam’ bubble is better than conventional foaming systems - it is lighter.
A heavy body of foam from conventional foamers is made up of many foam bubbles, all inconsistently sized. Many of these bubbles will be quite large – larger than i-spraywash foam bubbles. These large bubbles are also heavy. And the law of gravity means that they drop to the ground far more rapidly than the small, lightweight bubbles of the i-spraywash Active Foam.
Consequently, conventional industrial foaming equipment does not work as effectively as it could. Instead of clinging to the surface, allowing the chemical to work, a high percentage of foam drops quickly to the ground, going to waste.
It is essential that users understand this fine foaming principle, and do not mistakenly disregard the low level of foam as insufficient. You can see the proof of this foaming principle in the below image. The image compares conventional foamers immediately after application, compared with two minutes later. Notice how the i-spraywash Active Foam is clinging to the wall far better.
In some cases, it will appear that there is no i-spraywash foam left on the surface. However, if you inspect the area closely, rubbing it with your finger, you will feel that there is still chemical on the surface.
While you can adjust the foam dilution of i-spraywash on the gun, it is not necessary to leave a ‘completely white’ surface. Excessive foaming is simply chemical wastage and will not improve cleaning effectiveness.
We must also look at the speed of rinsing with the i-sprashwash . Compared to conventional foaming systems, the i-spraywash is significantly faster – again – due to the Active Foam. The thick foam generated by conventional commercial foaming systems is difficult to rinse. More water and time are required to move the foam to the drainage area and effectively drain. Instead, the foam tends to build up and ‘sit’ on top of the drain, rather than pass through it. Alternatively, the fine active foam bubbles generated by the i-spraywash move more quickly and easily across the floor, speeding up the rinse process and using less water.
The correct i-spraywash cleaning method
The i-spraywash must be used properly for optimal results:
1. Area of application: If the surface is drying before you get to rinse it, you are foaming too large an area before you begin rinsing. This is not unique to i-spraywash. This applies to any foaming gun or system. Different areas will dry faster depending on airflow, surface texture and porosity, ambient temperature, etc. If the surface is drying before you begin to rinse, reduce the area you foam before you start the rinsing process.
2. Speed of Application: To achieve the labour savings and cost efficiency benefits of i-spraywash, apply the foam at a rate of 1 sqm per second. Users must be trained to work at this speed as it is faster than average. When operators get used to this speed, you’ll start to see the efficiency of i-spraywash as a cleaning method.
The initial product introduction and training must be a supervised process. Otherwise, the true efficiency of the product will not be realised. Further, the cost will be unnecessarily high due to needless use of chemical.
Operators must be adequately trained in application speed, correct dosage and cleaning methods. Appropriately used by trained staff, the i-spraywash is proven to be an extremely straightforward and efficient cleaning method.
Read: Top commercial vacuum brands in Australia and New Zealand.

i-spraywash features:
- Designed for fast cleaning of large surfaces
- Save up to 50% work time
- Ergonomically friendly
- 2-3 x lighter than conventional liquid cleaning systems – ideal for any operator
- Save time and money
- Environmentally friendly
- Makes commercial cleaning and disinfecting a breeze
See the Advantages of Active Foam vs a Traditional Foaming Gun

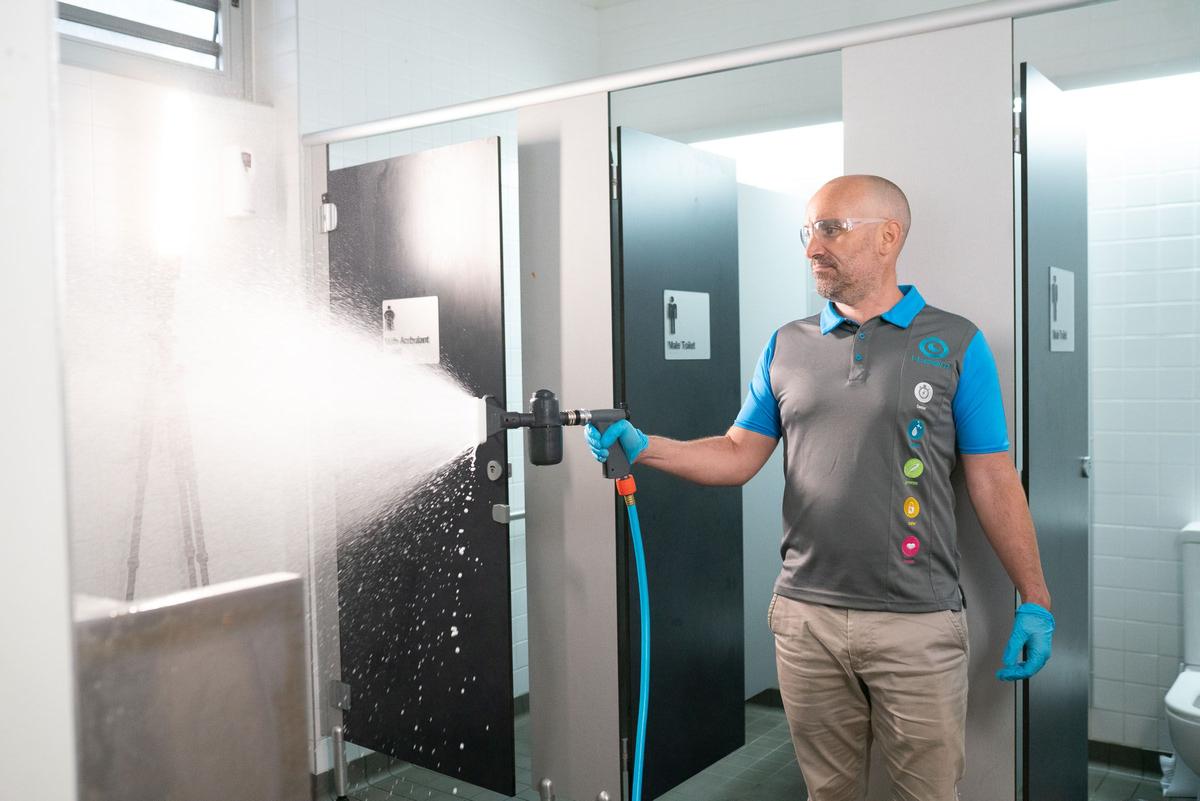
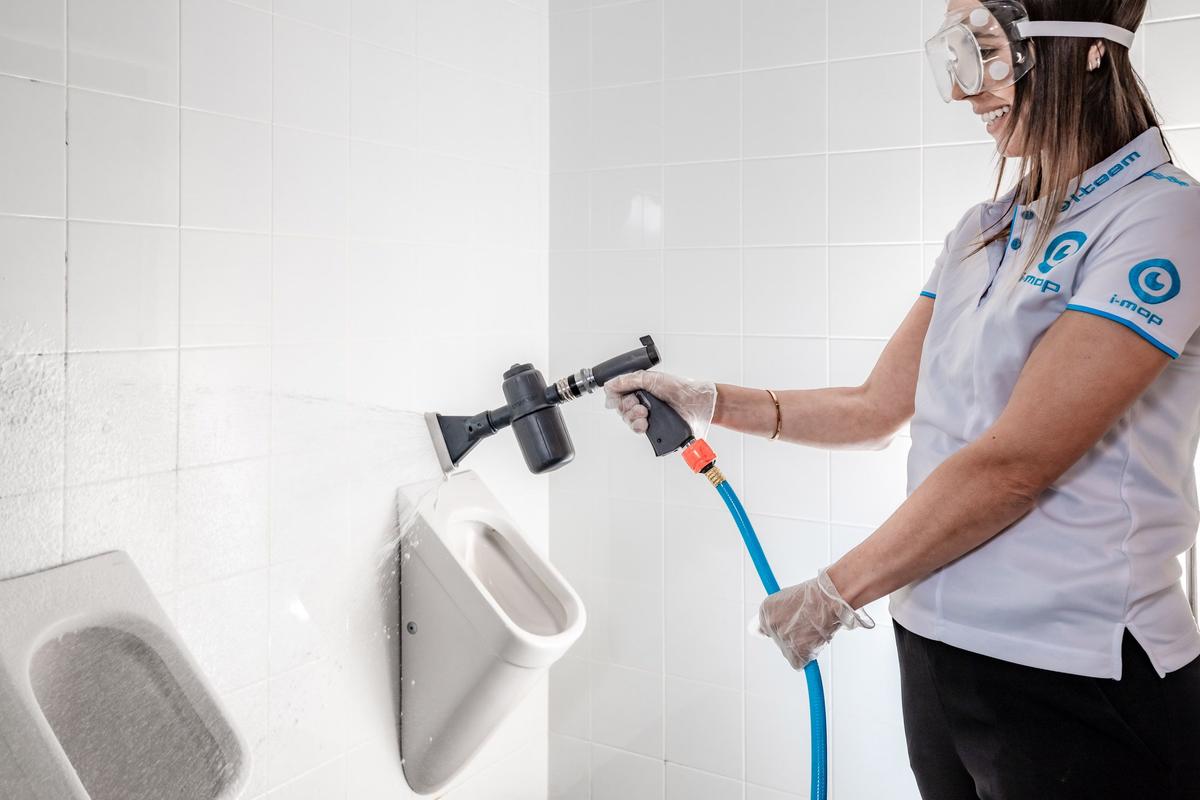
Products featured in this Case Study
Media & Insights
Join the movement that’s changing what clean means.
Be part of a cleaner world. Get a live demo at a time that suits you.
Get in Touch