You are reading: Better Manage OH&S In Your Commercial Cleaning Process
01 September 2022
4min read time
Brooke Payne
Better Manage OH&S In Your Commercial Cleaning Process
Share:
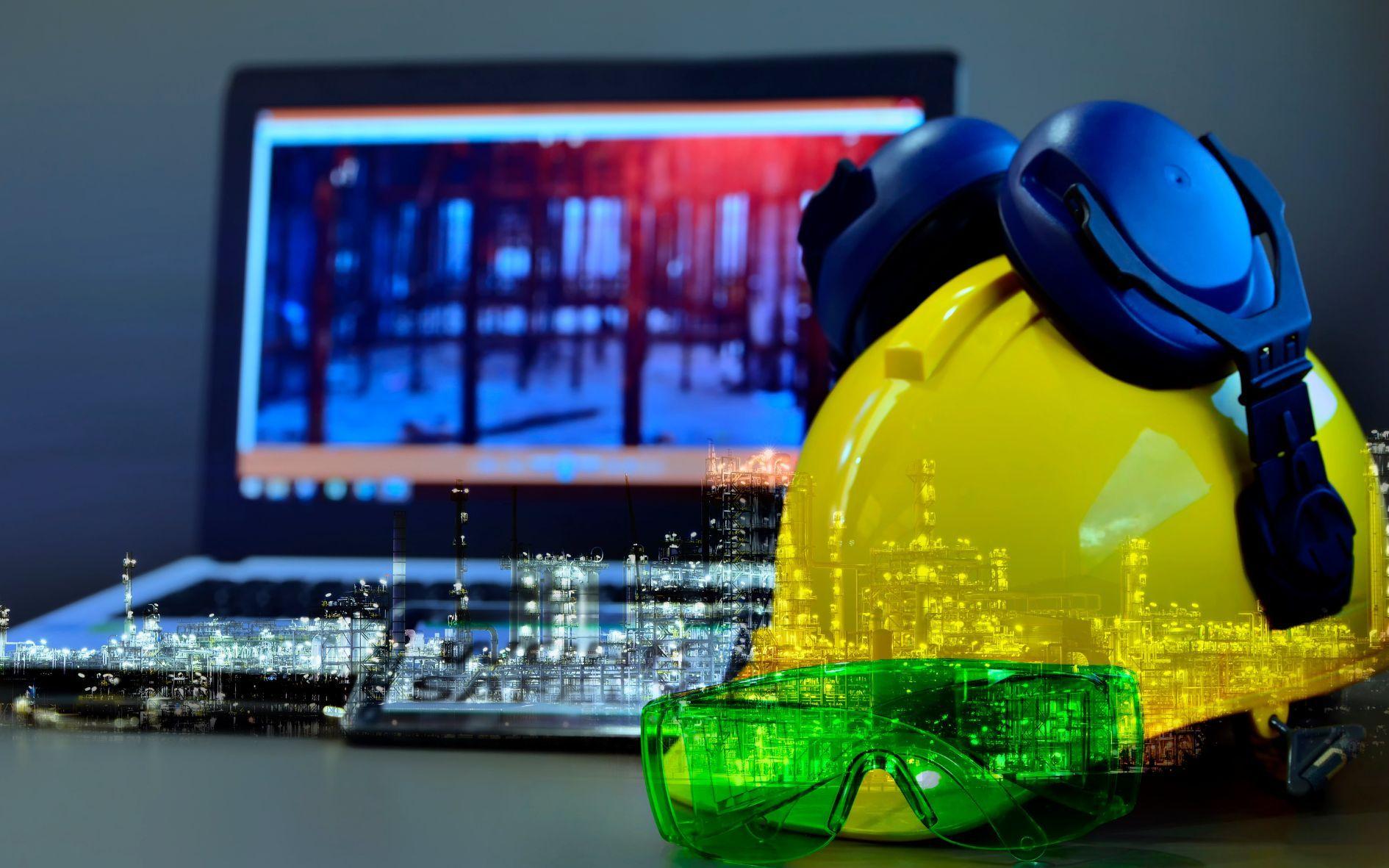
Key Insights
- In Australia, over the course of 12 years from 2003, slips, trips and falls accounted for 23% of serious claims, and were caused by environmental factors 56% of the time
- Lifting, pushing, pulling or bending, accounts for a significant 24.2% of all injuries
- Implementing innovative cleaning processes and equipment can massively transform the way you handle safety in your business
Cleaning commercial buildings shouldn’t have to be dangerous.
Maintaining hygiene standards in large commercial buildings involves a wide range of cleaning routines and, as a result, often poses OH&S issues. Workplace hazards, manual handling and slippery floors all represent risks to staff and customers in a commercial cleaning space. In Australia, over the course of 12 years from 2003, slips, trips and falls accounted for 23% of serious claims, and were caused by environmental factors 56% of the time.
Find out the steps you can take to better manage occupational health and safety in your commercial cleaning processes.

Take care with heavy equipment
Heavy equipment poses a major safety risk when it comes to commercial cleaning. In a 2018 study, the Australian Bureau of Statistics found that the most common cause of work-related injury or illness was ‘Lifting, pushing, pulling or bending’, accounting for a significant 24.2% of injuries.
Often, a whole suite of heavy and cumbersome cleaning products are involved in commercial cleaning. This can cause massive strain on cleaning staff.
Autoscrubbers, while delivering better cleanliness, are often too large to be used in small places or high traffic areas. In this case, we often resort to traditional mopping, which don’t adequately do the job and can, again, cause strain.
That’s where the i-mop comes in.
i-team has created the innovative i-mop: a floor scrubber dryer specifically designed to be better, safer and greener. It reduces time involved in cleaning and reduces the necessity of cleaning staff having to move backwards and forwards, by having a long charging life and a lightweight design.
The i-mop is designed to be easy to use, lightweight and can be utilised with one hand, which makes it more efficient. It’s the power of an auto scrubber with the agility of a flat mop.
Reduce slipping hazards
Floors are left slippery after mopping and, often, not even clean - dirty water is pushed around and left to dry. The i-team’s i-matt also reduces slip and fall hazards when cleaning floors, by providing an easy-to-use mat that isn’t invasive.
In addition, traditional mopping methods merely spread around soil and contamination rather than removing it. Our floor scrubber dryer, the i-mop, dries floors as soon as they are cleaned. It’s designed to scrub floors clean and then leave it dry within seconds.
This means that there’s no unnecessary amount of water on the floor and it can all be handled with one machine. That is cleaning excellence.

Be conscious of electricity and cables
A key part of electricity management and safety in cleaning is monitoring equipment, to ensure that it’s not damaged, and working with waterproof electric appliances.
If you’re using outdated or damaged electric cleaning equipment such as vacuum cleaners or floor scrubbers, there could be serious safety ramifications.
The i-team product suite utilises battery-powered equipment instead of 240v electric equipment. This reduces the risk of electric shocks, ensures that there are less trip hazards by trailing cables, as well as a reduced chance of damage to furniture and walls from cables.
All of the i-team’s batteries are easily rechargeable.
Light and space
Light is a prevalent problem for commercial cleaning staff. Some areas may be darker than others, and cleaning staff need mobile lights to help light their way, maintain safety and reduce chances of injury.
Our i-light is a battery-powered LED work light, which is a durable and reliable unit. It fits easily on any of our i-land trolleys, reducing the necessity for energy usage, as well as ensuring that cleaning staff have light wherever they go.
Measuring clean for better safety
Think your surfaces are clean enough? You can know just how effective your cleaning methods are with the i-know program.
You might be surprised.
i-know is i-team’s ATP Testing solution, which establishes objective hygiene benchmarks by using specialised equipment, swabs, software and consultation to help you measure cleaning effectiveness.
ATP (Adenosine Tri-Phosphate) is found in all organic matter. Monitoring the amount of ATP remaining on surfaces after cleaning quantifies just how effective your cleaning is.
Your cleaning processes might not be as effective as you might think, and especially in current times, you need to be able to trust in your hygiene standards. i-know ensures maximum levels of safety and cleanliness.
Read: How to maintain the i-mop by checking for wearing parts.

Overall safer environments
The point of streamlined cleaning in industries is to not only protect the customer, but also to protect cleaning staff. Traditional mops and buckets are slow, heavy and cumbersome, and can cause injury to staff. Implementing innovative cleaning processes and equipment can massively transform the way you handle safety in your business.
Using the i-team suite of commercial cleaning equipment cuts out difficulty and danger from the commercial cleaning process. We elevate hygiene standards while also improving safety, productivity and overall environmental impact. We transform the way you see ‘clean’, because we know that you, your staff and your customers deserve the best.
You can find out more about the i-team suite here or contact us here for more information.
Common Questions Answered
1. What are the key elements of an effective OH&S program in commercial cleaning?
Answer: Key elements include risk assessments, employee training, clear communication of safety procedures, regular equipment maintenance, and the use of personal protective equipment (PPE) to ensure a safe working environment.
2. How can technology be leveraged to enhance OH&S compliance in cleaning operations?
Answer: Technology can improve OH&S compliance through tools like digital training platforms, mobile apps for reporting hazards, and automated systems that monitor equipment safety and maintenance schedules, ensuring adherence to safety standards.
3. What role does employee training play in managing OH&S in commercial cleaning?
Answer: Comprehensive employee training is crucial for instilling safety practices, raising awareness about potential hazards, and ensuring that staff are familiar with emergency procedures, ultimately reducing workplace accidents and injuries.
References
SafeWork Australia – Work Health and Safety in the Cleaning Industry
URL: https://www.safeworkaustralia.gov.au/campaign/cleaning-industry
Cleaning & Maintenance Management – OH&S Best Practices
URL: https://www.cmmonline.com/articles/ohs-best-practices-for-cleaning
Facility Cleaning Decisions – Managing Safety in Cleaning Operations
URL: https://www.cleanlink.com/facilitymanagement/article/Managing-Safety-in-Cleaning-Operations--20788
Products Featured iInside this Article
Media and Insights
Join the movement that's changing what clean means.
Be part of a cleaner world. Get a live demo at a time that suits you.
Book a Demo